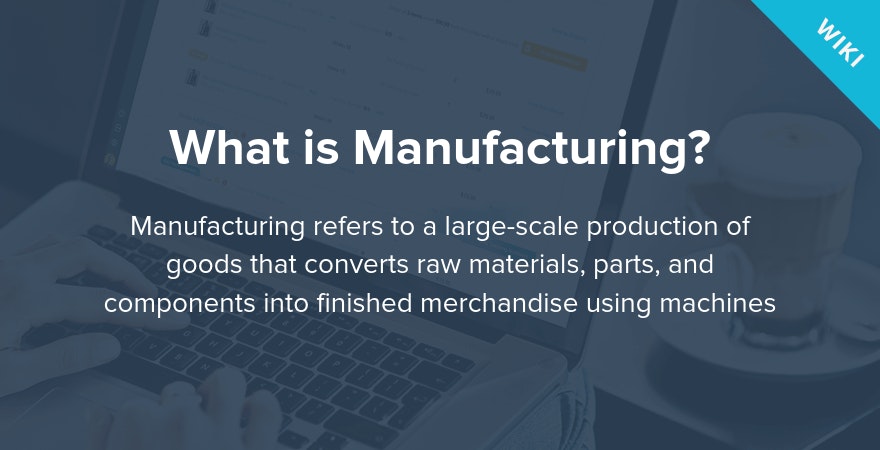
Manufacturing
What is Manufacturing?
Manufacturing refers to a large-scale production of goods that converts raw materials, parts, and components into finished merchandise using manual labor and/or machines. The finished goods canbe sold directly to consumers, to other manufacturers for the production of more complex products, or to wholesalers who distribute the goods to retailers.
In theUS manufacturing represents 15% of its economic output, including automobiles, aerospace, machinery, telecommunications.
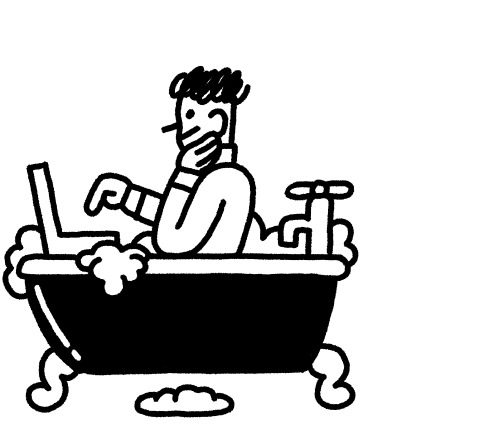
Start your 14-day free trial on Shopify today!
Start Free TrialWhat is a Manufacturing Business?
A manufacturing business is any business that uses raw materials, parts, and components to assemble finished goods. Manufacturing businesses often employ machines, robots, computers, and humans to produce the merchandise and typically use an assembly line, which enables a product to be put together step by step, moving from one workstation to the next.
Manufacturing businesses can choose to sell their products directly to consumers, to other manufacturers, to distributors or towholesalers.
What’s the Difference Between a Manufacturer and a Wholesaler?
A manufacturer is responsible for assembling the final goods, such as laptops, fridges or watches, or producing parts and components that other manufacturers use to produce more complex products like cars or aircraft. A wholesaler, on the other hand, is a middleman between a manufacturer and a retailer (or end consumer). It buys products in bulk from the manufacturer and resells them in smaller quantities for a higher price.
Types of Manufacturing Production
There are three main types of manufacturing production: make-to-stock (MTS), make-to-order (MTO), and make-to-assemble (MTA).
Make-to-Stock (MTS)is a traditional manufacturing strategy that relies on past sales data to forecast consumer demand and plan the production activity in advance. The drawback of this strategy is that it uses past data to predict future demand, which increases the likelihood of the forecasts being off, leaving the manufacturer with too much or not enough stock.
Make-to-Order (MTO)allows customers to order products that are customized and manufactured to their specifications. The manufacturing process begins only after the order is received, so the waiting time for the customer is longer, but the risk of excessive inventory is cut out.
Make-to-Assemble (MTA)is a strategy that relies on demand forecasts to stock the basic components of a product, but starts assembling them after the order is received. It’s a hybrid of MTS and MTO approaches. Customers can customize the products and receive them quicker because the manufacturer has the basic components ready, but if orders don’t come in, the manufacturer is stuck with a stock of unwanted parts.
All three types of manufacturing businesses have certain risks involved. Producing too many goods leads to financial losses as money is tied up in unwanted stock; producing too little means not meeting the demand, which can cause the customer to turn to competition and induce a drop in sales for the manufacturer.
To reduce the risks, any type of manufacturing business should focus on keeping production costs low, maintaining good quality control and investing in excellent sales management.
Want to Learn More?
- What Should You Sell Online?
- Best Dropshipping Products to Sell in Fall
- 20+ Trending Products to Sell
- Best Dropshipping Products to Sell in Summer
Is there anything else you’d like to know more about and wish was included in this article? Let us know!